Filter deposits
Modern gears, motors or hydraulics - they are all designed to become more compact and energy efficient yet deliver a higher performance. This trend often also comes with increasing operating pressure and more precision-manufactured components. Higher demands are made of the quality and purity of the lubricant. Consequently, many systems are also equipped with increasingly finer main and secondary current filters. Accordingly, the proof of external and dirt particles in oil as well as the determination of the purity class have an increasingly decisive role to play in lubricant analytics. Admittedly, caution is also advised when it concerns oil purity and filtering...
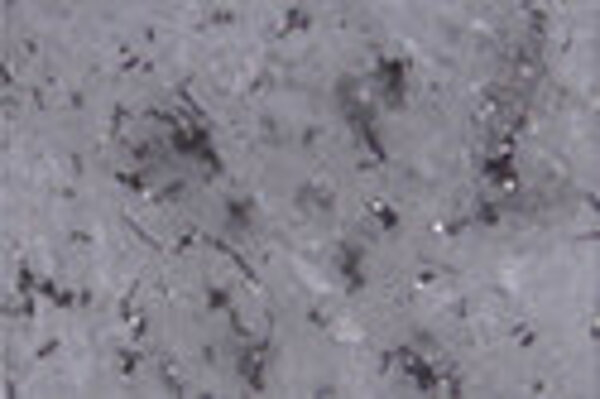
There are three critical issues to consider:
- Trend analyses show "everything is in the green". Operators often tend to extend the inspection intervals if the high degree of oil purity they are aiming for is confirmed. However, if changes suddenly occur in the oil, they are then no longer detected in time.
- The fine filters can be so effective that, in some cases, active substances in the oil can also be filtered out. This mainly affects additives such as silicone defoamers, viscosity index improvers or detergents. If they get caught in the filter, the performance of the lubricant can deteriorate.
- Abrasion particles from wear processes or foreign particles introduced from outside can and should be retained by the filter. During sampling, such particles do not enter the sample vessel. This deprives the oil of important information carriers that would otherwise provide information about problems during lubricant analysis.
A used oil from a system with optimum filtration thus often only reflects an incomplete picture of the oil and system condition. In these cases, only the analysis of the filter residue completes the actual findings.
A case study in practice
The person accountable had been aware of the critical state of the gearing of a highly loaded rolling mill drive in a cement mill for a long time. The ordered replacement gear wheels, however, were only be assembled during the major revision some months later in order to avoid an operational stoppage. The gear was closely monitored by lubricant analyses. The attrition values determined were measured over weeks in the tolerable range and alarming deviations were not recorded. However, a filter change was then signalled on the basis of a changed differential pressure. The maintenance workers noticed a suspiciously high loading of the filter with metal abrasion. During an inspection made at short notice, a tear was discovered - along with many outbreaks (pittings) - which indicated an imminent tooth-breakage. The gear had to be exchanged as quickly as possible.
Had the lubricant analyses failed in this case? Why hadn‘t the laboratory flagged this up in time? Could something like this happen again?
The maintenance workers wanted to know precise details. They sent in an oil specimen again. This time too the investigation results were within the tolerated range. Both the PQ index for the total amount of magnetisable iron in the sample and the portion of iron particles determined with the ICP spectometry, which are smaller than 3 µm were not alarmingly high.
But quite different values were to be seen in the filter deposit investigation. For this purpose, the deposits of a 50mm x 50mm piece were extracted in the laboratory using solvent. Here, metallic wear particles with a diameter of up to 80 µm and large dirt particles with a diameter of up to 100 µm were manifested.
Here, a residue analysis and a microscopic particle count usually provide a good statement. If the particles should still be analyzed even then, OELCHECK offers the SEM-EDX examination as a further possibility since 2018. In such special cases a reliable examination for the material compositions desired. We recommend: Let us advise you about the requirements and result possibilities.
The filter deposits, and not the gear oil, were the deciding data media in this case.
However, it was not simply the proof of wear that was conveyed here. The large dirt particles had to have penetrated into the gear oil from the outside. During a further gear examination, it was ascertained they had got in through a defective ventilation filter. From this, the cause of wear was also found.
Also read Extract filter specimens correctly
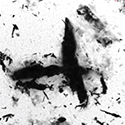
OELCHECKER Winter 2013, page 5