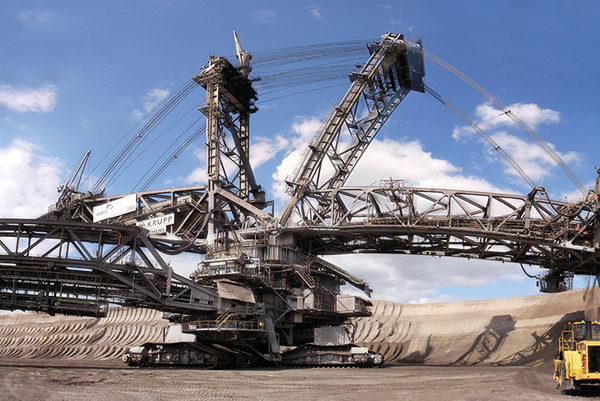
Think big and act sustainably – Lubricants for mining machines
Year of publication: 2025
Whether it’s a brick, the cement bag in the DIY store, a pair of steel pliers or the mobile phone in our hand: The materials needed to make them could tell stories. But who thinks of the mining excavator or the wheel loader that is in operation around the clock to extract the necessary raw materials when they think of the everyday use of these things.
Even the size of the construction machines we encounter on one or the other construction site when passing by, whether excavators, wheel loaders, crawlers or even tippers, may impress us. Compared to an excavator from the open pit mine or quarry, they look like dwarves. Mining machines are in a league of their own in terms of size.

From oil sample to analysis – how we ensure the highest quality
Year of publication: 2025
In the last OELCHECKER, you reported on the importance of taking an oil sample from the machine or system correctly. What happens when our oil samples reach the OELCHECK laboratory?
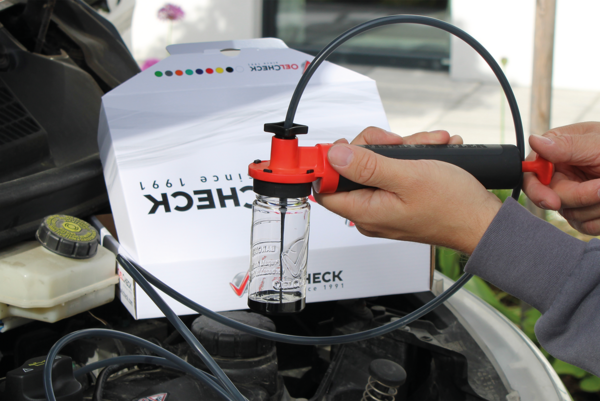
Sampling – Basis for reliable analyses and diagnoses
Year of publication: 2024
Correct sampling is a prerequisite for meaningful laboratory results and reliable decisions. Even state-of-the-art testing equipment and experienced evaluation engineers cannot realise their potential if the basic rules of professional sampling are disregarded out of ignorance.