Fluxes and coolants – Not the best of friends
Publication year: 2023
Aqueous coolants are extremely important in ensuring the safe operation of engines, converters and many other systems. But during use, their condition changes due to ageing and contamination. In the past, examinations using handheld devices and measuring strips were carried out on site to check antifreeze and heat transfer properties and to find signs of degrading basic protection additives.
Monitoring with OELCHECK all-inclusive analyses goes far beyond this and ensures a high level of safety when using coolants. This is because, provided that regular analyses are carried out, we can now not only detect existing corrosion, but also interpret indicators of its future formation and warn of impending damage. The fluxes used when soldering the coolers also continue to play a key role here!
Engines, converters and many other technical components need to be protected against overheating. The heat lost during operation is dissipated, thereby cooling the components. This is done with the help of air, water, cold mixtures with special salt compounds or coolants, which in most cases are based on glycol. The latter are not just used for radiators in motor vehicles. Aqueous glycol-based coolants are also used in cooling systems for wind turbines, locomotives, stationary engines (such as in energy generation using biogas) or in power supply converters.
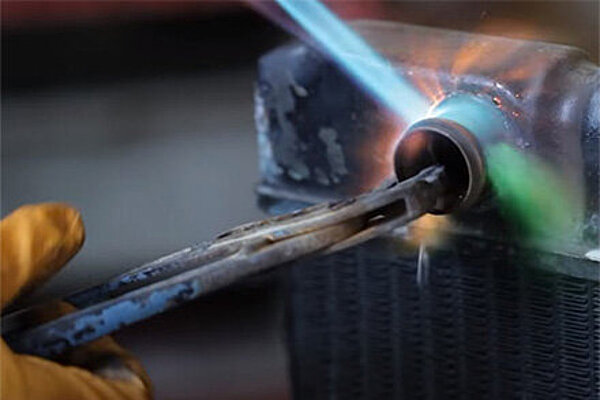
Corrosion is a danger to any cooler
Heat exchangers are predominantly made of aluminium, while their connections and supply lines are made of aluminium, stainless steel, copper or brass. Aluminium is a good heat conductor, but it can also corrode. In the case of coolers, oxygen corrosion is the main concern. With this form of corrosion, the metal decomposes in the presence of oxygen and a conductive fluid. Different variants of corrosion can occur in this process:
- Surface corrosion: occurs on parts or even the entire surface of the material.
- Galvanic corrosion: is based on an electro-chemical reaction between two different metallic materials, such as aluminium and steel.
- Pitting corrosion: is an aggressive form of corrosion that produces holes or cavities. It is mainly caused by halides such as chloride, fluoride and bromide.
- Crevice corrosion: occurs in gaps that are not sealed, such as overlaps, attached bars and in the case of non-continuously soldered or welded seams.
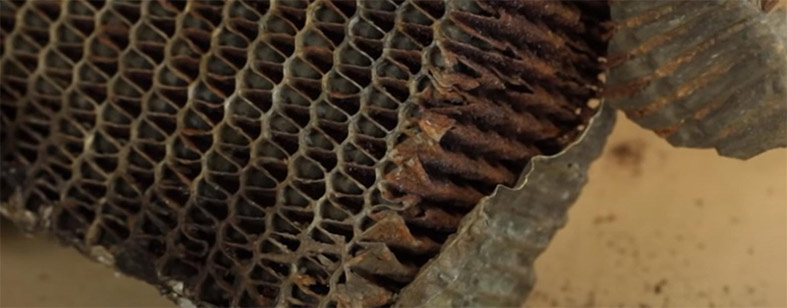
Coolants and protecting against corrosion
Coolants and antifreeze agents have a variety of tasks. They are intended to ensure optimum heat supply and dissipation as well as to protect against corrosion, cavitation, foam formation and deposits. At the same time, they must not attack the metals and sealing materials installed in coolers. Up to 10% of a coolant concentrate consists of additives whose main task is to protect the metallic surfaces in the cooling circuit against corrosion.
Over time, additives for corrosion protection have been continuously developed to meet the increased requirements for durability, material diversity and environmental and health protection. While older formulas consisted of just a handful of components, which could often be detected using simple measuring strips, today's formulas contain a complex combination of organic and inorganic salts, which can only be measured and evaluated in the laboratory.
OELCHECK monitors and makes a discovery
OEMs and operators are increasingly focusing on consistently monitoring coolants by means of laboratory analyses. OELCHECK examines all important parameters of the fluids and ensures their functionality over a long period of time and thus the safe operation of the refrigerated units.
The following are critically examined:
- The condition of the coolant, its ageing or degradation products, such as glycolate, oxalate and formate
- The (base) water quality
- Changes to additives
- Contaminants
- Elements indicating corrosive wear
Any existing wear due to corrosion is primarily reflected in the content of metals in the examined coolant. But are there certain substances that promote corrosion? Can these also be detected in the coolant in order to identify a tendency towards impending corrosion at an early stage? And how do the individual parameters correlate?
Fluxes affect the coolant and the entire system
It has long been known that some substances can promote corrosion. Some of them, such as chloride or sulphate, come from the water mixed with the glycol. As a rule, the requirements for the base water are therefore described in every operating manual for coolants. Substances that penetrate from the outside are also often considered. On the other hand, "built-in" contaminants are very often forgotten, either from assembly (assembly pastes and corrosion protection oils) or from production (processing fluid and flux). Fluxes have proven to be particularly critical.
Potassium, aluminium and fluorine are constituents of the chemical compound K1–3 Al F4–6 (potassium aluminium fluoride), which is very commonly used as a flux when brazing aluminium. In this CAB process (Controlled Atmosphere Brazing), the individual components are joined together using a solder. The solder usually consists of an aluminium alloy whose melting point is significantly lower than that of the components. The purpose of the flux is to remove the natural oxide layer present on all aluminium surfaces. This layer would negatively affect the solder joint mechanically and in its electrical properties. In addition, the flux must allow the solder to flow freely and prevent the formation of a new oxide layer on the surfaces.
Fluxes made from a compound of potassium, aluminium and fluorine are not corrosive in themselves, but remain in a thin layer on the aluminium after the components have cooled down. In most cases, too much flux is used, as too small a quantity leads to unstable solder joints and thus possibly to non-compliance with strength values and/or part specifications. But excessive flux does not initially have any negative effects on the soldering process or on the component itself.
This means that fluxes can be detected in almost all cooling systems with soldered aluminium components. In increased concentrations, however, they activate metal surfaces and break down corrosion inhibitors in the coolants. This creates favourable conditions for corrosion to occur. What's more, the fluoride promotes pitting corrosion, as is known from chloride. In many cases, coolants contaminated with flux residues are also subject to increased degradation products of glycol and a decreased pH value of the liquid in the laboratory.
A high content of potassium, aluminium and/or fluorine in a coolant generally promotes the formation of corrosion. In laboratory analysis, additional anomalies are also always found. These can affect various parameters in different combinations. There are no universal laws here. Each case must therefore be considered individually and always in conjunction with all other values of an analysis. The interactions between materials, solder, flux and coolant in the respective cooling system must also be taken into account.
The flux problem has been known in the automotive industry for around 20 years. Other areas are only just beginning to experience it. In wind power, for example, more and more converters are being switched from air to water cooling due to the increasing output. Here, OELCHECK tribologists have been able to help a large wind turbine manufacturer develop a strategy for dealing with flux loads from coolants.
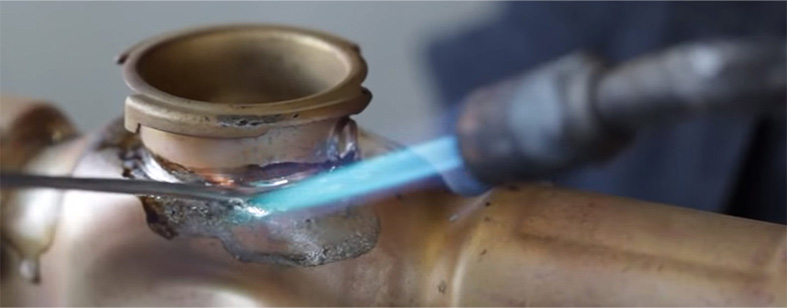
Remedy and prevention
Due to the poor solubility of fluxes in cooling water, contamination with them cannot generally be eliminated, even with several coolant changes.
Other measures, such as switching to a different flux or cleaning, are not easy to perform or have their pitfalls. Due to this problem, coolant manufacturers have developed solutions including "flux-tolerant coolant additives". These prevent the release of harmful components in a variety of ways. But unfortunately, these fluids are not the silver bullet they are hoped to be against the issue of flux. This is because they only work against potassium aluminium fluoride-based fluxes.
As such, OELCHECK tribologists have determined that some cooler manufacturers have switched from "conventional" fluxes to products with formic acid, for example. Restrictions on the fluoride content of components can thus be circumvented, for example. Unfortunately, the analyses show that the changed flux continues to lead to additive degradation and corrosion. The number of cases is still low, but OELCHECK tribologists will continue to monitor further development closely.
However, a worryingly high concentration of fluxes in coolants can be prevented:
Prevention includes regular checks using OELCHECK all-inclusive analyses!
Five tailored OELCHECK all-inclusive analysis kits with different combinations of selected test methods are available for monitoring coolants.
We recommend a regular check with an Advanced or Premium all-inclusive analysis kit for reliable early detection of flux contamination and/or impending corrosion due to contamination with flux.
How prevention works!
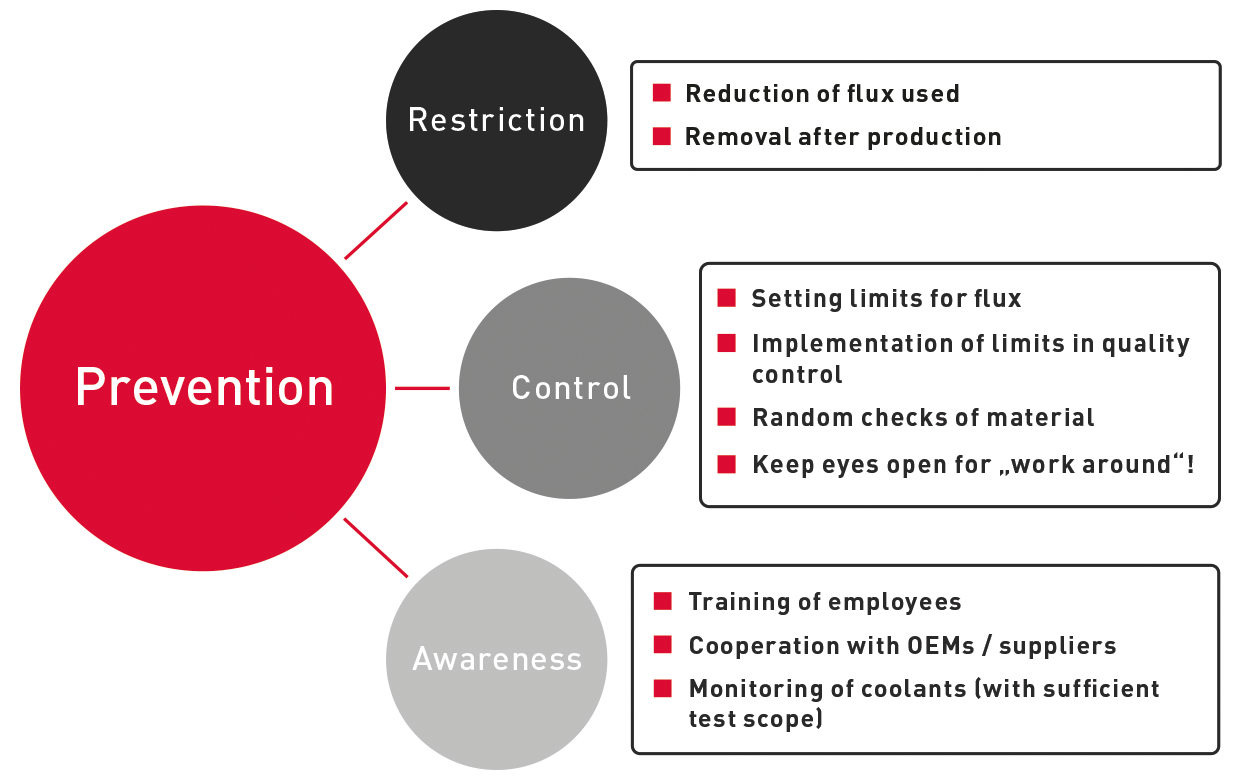
OELCHECKER Winter 2023, page 4