Analysis kits for refrigeration compressor oils
Our test procedures selected for analysing oils from refrigeration compressors have proven themselves time and time again over the years. However, we have further optmised the tests, our laboratory equipment and the sample containers for these products yet again. It‘s not just the users of modern synthetic refrigeration machine oils who are benefiting!
New analysis kits VK1 and VK2 for refrigeration compressor oils identify:
- Wear metals: iron, chrome, tin, aluminium, nickel, copper, lead and molybdenum
- Additives: calcium, magnesium, zinc, phosphorus, barium, boron and sulphur
- Contaminants: silicon, potassium, sodium and lithium
- PQ index
- Optical check (colour change, visible particles)
- Viscosity at 40°C and 100°C as well as the viscosity index
- Oxidation
- Special outgassing process
- Water content according to Karl Fischer
In addition to the tests above for analysis kit VK 2:
Neutralisation Number (NN) or Acid Number (AN) or Base Number (BN)
Refrigeration compressor oils should lubricate, minimise friction, protect from wear and corrosion, cool, clean, prevent deposits and create a seal or reduce any leakage flow in the compression chamber. However, for the most part they also come into direct contact with the refrigerating agent. A refrigeration machine oil therefore has to work in harmony with it as much as possible. Impurities from seal materials or negative impacts from moisture or even water are one of the criteria for an oil change or additional oil servicing measures. The temperatures during compression of the gaseous refrigerating agent of up to 120 °C can significantly accelerate oil oxidation, hence its ageing. During an oxidation process, mostly acids form in the oil which can have a corrosive effect on the compressor components, particularly if there is any residual moisture.
The production capacity of the refrigeration compressor oil and its interaction with the refrigerating agent have decisive effects on the service life of the compressor. Therefore, regular lubricant analyses are vital. They provide information on the condition of the oil and the complex chemical reactions that have taken place in the compressor oil. If necessary, any potential damage and disruptions to operations can be counteracted.
There are special OELCHECK analysis kits for the extremely important task of monitoring refrigeration compressor oils. When the test processes in the kits were compiled, not only were our experience and the recommendations of previous compressor and oil manufacturers taken into consideration, but also the specifications of work group E-DIN 51503
Acids or bases in refrigeration machine oils
The Neutralisation Number (Acid Number or AN) provides information on the level of mineral acids as well as water-soluble and insoluble organic acids in a refrigeration compressor oil. Mineral acids, such as hydrochloric or hydrofluoric acid, are formed through the decomposition of halogen refrigerating agents or upon interaction with the refrigeration machine oil. Organic acids result from the oxidation of refrigeration machine oils and the decomposition of ester oils. All of these acids lead to the corrosion of the metallic materials in refrigeration systems, promote oil ageing and cause unfavourable changes in the electrical isolation values of motor compressors.
The Base Number (BN) provides information on the level of alkaline substances in the oil. They are caused by oxidation in ammonia refrigeration systems in the case of thermal loading. Inside the compressor they lead to oil silting and on the hot side, in pressure chambers and on valves, to carbonaceous deposits.
New sample containers
With pre-paid kits VK1 and VK2 for oils from refrigeration compressors, from now on, customers are provided with newly designed gas-tight 100 ml sample containers made from glass with a metal lid. They are suitable for all oil types and refrigerating agents. In addition, they can withstand the internal pressure, which can build up due to residual refrigerating agent in the sample. The sample amount is extracted via the oil outlet provided by the manufacturer in the compressor circuit. If the sample foams quite heavily, some of the gas can be released from the refrigerating agent prior to sealing. Gas should not be released if a synthetic compressor oil is used and/or ammonia is used as a refrigerating agent. The container must be carefully sealed immediately since these substances are extremely hygroscopic and can soak up moisture from the air even if the contact with the atmosphere is short.
Extensive sample preparation
The individual process steps were redesigned for refrigeration machine oils. A partial quantity of max. 5 g is directly extracted when the sample container is first opened. That way, the exact water content can be ascertained according to the Karl Fischer method. To ascertain the other values, the proportions of refrigerating agents in the sample must be removed. The opened sample containers are therefore clamped in a gas-tight appliance. After the samples are warmed to 80°C, inert gas flows through the oil until no more refrigerating agent can be found in the waste air flow. Only after this process, which lasts for more than an hour, has been completed, is the sample ready for further extensive laboratory tests.
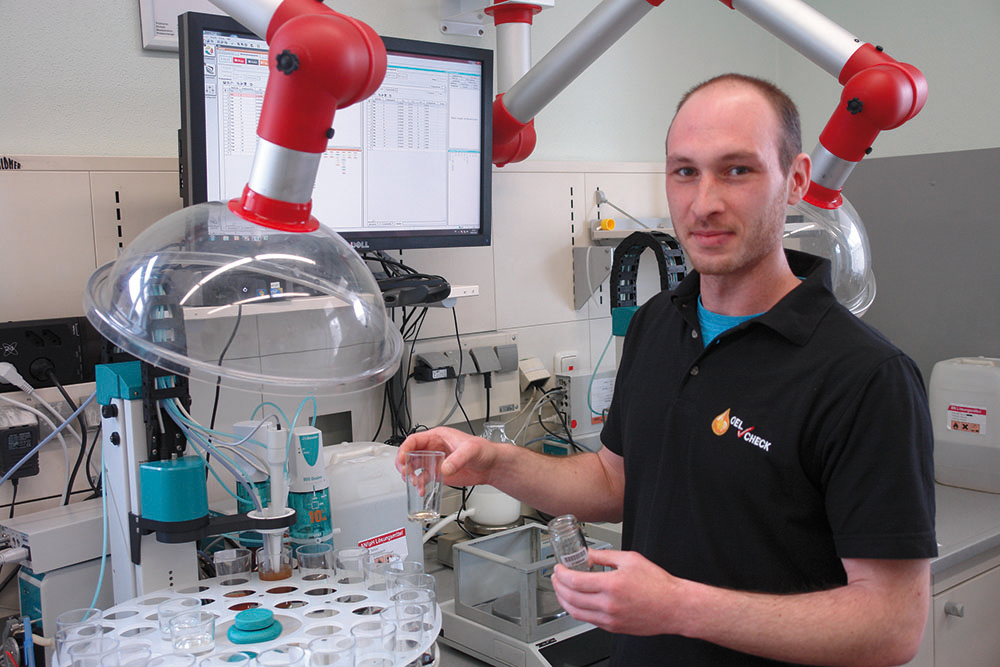
ÖlChecker Winter 2012, page 3