Lubricants in the food industry
Year of publication: 2006
Wherever there may be occasional or even technically unavoidable contact between the lubricant and food products, only lubricants that are named in a list published by the NSF under heading H1 should be used. The NSF (National Sanitation Foundation) is an independent organization that has been involved in certifying products, writing standards and conducting tests to protect food, water and consumer products in the USA since 1944.
However, using an NSF-H1 food grade lubricant is not a carte blanche. A foodstuff contaminated or polluted with lubricant must not be placed on the market even if this lubricant has H-1 approval.
The use of lubricants with NSF-H1 certification has long been mandatory in the food industry. Recently, their use has also been required by an EC directive in the production of animal feed. However, although such oils and greases are not allowed to contain the usual metal-organic EP additives, e.g. based on zinc or molybdenum, they often have to perform better in food production than lubricants in other areas of industry. This is because water, steam and cleaning agents are a problem for them everywhere. In meat processing, they have to be resistant to animal fats, blood and salts. In the beverage industry or in the production of canned fruit, fruit acids attack them. Flour dust or sugar affect them in the baking industry. Added to this are often extremely high temperatures, as in canning, or extreme cold, as in the manufacture of frozen products.
The formulation of food grade specialty lubricants is therefore relatively complex. Since they may only be manufactured from components listed as safe by the FDA (Food and Drug Administration) or NSF, they can occasionally reach their technical limits. For this reason, the following applies even more than when conventional lubricants are used: Extensive technical knowledge and practical experience are essential for formulating and selecting the optimum lubricant.
.
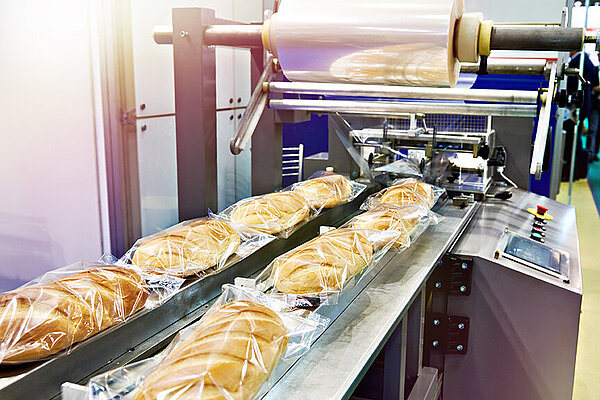
Table of contents
Safety is the trump card
Lubricants used in the production of food, feed or beverages must be neutral in taste and odor, but most importantly, they must be safe for human health.
With a product certified by the NSF according to H1, the operator plays it safe, because according to the NSF, only harmless raw materials may be contained in the lubricants. This applies to base oils, additives and active ingredients, but also to the thickeners in lubricating greases.
Either mineral oil-based technical or medical white oils or selected synthetic oils based on PAO, ester and polyglycol are selected as base oils. All additive combinations must be free of heavy metals, such as zinc or barium. But even approved additives such as phosphorus or sulfur are often limited in quantity.
Base oils and their properties
White oils are highly refined mineral oils with a high degree of chemical purity. Bleaching earth treatment gives the natural yellow oils a water-light color, hence the name. White oils, sometimes referred to as paraffinum liquidum, are available in technical and medicinal grades mostly in low viscosities. Medicinal white oils are mainly used as a base material for ointments and cosmetics.
Technical white oils, which are also compatible with known mineral oil-compatible materials, are mainly used for lubricants. However, pure white oils age relatively quickly if they do not contain oxidation-inhibiting additives. Therefore, in recent years, lubricants with synthetic base oils have been increasingly developed that are superior to mineral oil-based white oils in terms of oxidation stability and lubricity.
PAOs – polyalphaolefins are synthesized from crude gasoline or from gases (propane). In the refinery, individual ethene molecules are usually combined to form tailor-made ISO kerosenes with similarly long carbon-hydrogen chains.
PAO-based lubricants have several advantages over white oils:
- They have good viscosity-temperature behavior (VI of about 140 and more).
- They are very stable to oxidation and aging.
- They have a low evaporation rate.
- They are still liquid even at low temperatures.
- A disadvantage, however, is their relatively high price.
Esters are formed on the basis of a combination of alcohol and acid. Esterification can give rise to molecular chains with a wide variety of combinations. The main distinction is between saturated and unsaturated esters. Some types of compounds are relatively well biodegradable.
- Ester oils have a better natural lubricating effect than white oils.
- The viscosity-temperature behavior is similar to that of PAO oils.
- Saturated ester oils are relatively stable to aging even without the addition of additives.
- However, with increased water content, esters tend to hydrolyze.
- They are not always compatible with seals and coatings.
- However, they are also much more expensive than white oils.
Polyglycols are not actually oils in the conventional sense, but polyhydric alcohols. The starting product for their production is naphtha. Like water, they have a density of about 1 g/cm3 (mineral and synthetic oils of about 0.9 g/cm³). They are therefore usually very soluble in water and release water only with difficulty. Some types are also more rapidly biodegradable.
- Glycol oils have very good EP and lubricating properties.
- They are particularly suitable for non-ferrous metal and worm gear lubrication.
- They have very good viscosity-temperature behavior (VI above 200).
- They are also very stable to aging when used at high temperatures.
- However, they are not compatible with all seals and coatings.
- Disadvantage: Glycols are completely incompatible with other synthetic or mineral oils.
Basic rules for safe conversion
If a company converts the oils and greases for its equipment from conventional products to physiologically harmless H-1 lubricants, it is expected that everything will run at least as well afterwards as it did before. Long relubrication and oil change intervals due to good aging stability, high EP wear protection, compatibility with the previous lubricant or with seals and paints and, of course, NSF-H1 certification are demanded as a matter of course.
Today, in contrast to the past, "food grade approved" lubricants are available with high performance and a wide range of applications, albeit at a correspondingly higher price. But it is not enough for lubricant manufacturers to carry these products. Unfortunately, not many sales representatives have the experience necessary for optimal conversion, and often they cannot take the time to provide comprehensive advice to prospective customers, who often do not have huge oil sales. This is where the OELCHECK consulting service can often help.
Lubricant analyses provide timely information on impending damage, mixing or problems during changeover. This cost-effective tool offers additional security, especially during the changeover phase.
Special requirements
The quoted "basic rules" apply to all industries, areas of application and machine elements. In addition, there are still special requirements which must be taken into account, for example, when selecting gear, hydraulic and compressor oils.
Gears can be lubricated with oils based on mineral oil/white oil, polyglycol or ester. Today, PAO-based gear oils are a bestseller because they are usually well compatible with the residues of previously used mineral oils and also contain very effective EP additives.
In most cases, compliance with DIN 51517 alone is not sufficient to describe the performance of gear oils. Often, additional named approvals from the gear manufacturer or special wear tests, such as an FVA pitting test, are required. A thorough used oil analysis can quickly prove whether the wear protection behavior is really sufficient, even if a good FZG value is proven for the fresh oil.
Hydraulic systems can usually be re-oiled from mineral oil-based hydraulic oils to PAO H-1 oils without any problems. But despite good miscibility, it should be checked whether the additives of the oils are compatible with each other. Otherwise, foam may form or the air release properties of a mixture may become so poor that pump damage due to cavitation is imminent.
If a detergent HLPD or a zinc-containing HLP hydraulic oil was previously used, the re-oiling process should be controlled by laboratory analysis until the calcium or zinc value is below 15 ppm.
Rotary screw compressors often produce the compressed air for food packaging machinery. Oil mist constituents can enter food products with the compressed air. Since mineral oil-based compressor oils often only have a relatively short service life, synthetic H-1-based compressor oils should be given preference in the interest of longer oil change intervals. However, ester oils can become problematic in oil-flooded compressors or where there is a high water content.
Oil analyses not only show how long the oil can remain in use in each case, but also provide information about functioning water separation.
Lubricating greases
The conversion from conventional greases to H-1 greases is much more difficult than with oils. Bearings or lubrication lines can usually not be cleaned of the previous grease without problems or only with considerable effort.
Extreme care is also required when selecting suitable physiologically harmless lubricating greases. Especially here, advice should be given by an experienced sales engineer of the grease manufacturer. In case of missing information, the OELCHECK consulting service, which is subject to a charge, can help. The same basic rules as for oils apply to the procedure for converting the grease previously used to a grease with H-1 approval.
Be sure to clarify the following questions:
- Are old and new grease compatible with each other? Mixing greases with different soap bases (e.g. lithium with sodium) can often make greases extremely soft.
- Does the grease need to be completely replaced and the bearing thoroughly cleaned, or is it sufficient to lubricate through or relubricate at shorter intervals?
- What about temperature stability at high temperatures?
- In most cases, H-1 greases have shorter relubrication intervals due to their structure. How often and how much grease needs to be relubricated?
- Is the grease easy to convey in central lubrication systems?
- Can used grease analyses contribute to operational reliability or clarify unanswered questions?
Conclusion:
Lubricants that are NSFH1 certified are now available to supply machinery in the food industry, and they can also almost always perform as well as conventional products. Most lubricant manufacturers carry food grade products in their range, but not all have extensive experience or give an experienced consulting engineer the time to assist the customer with selection or conversion.
Please note: Follow our basic rules.
- Do not generalize hastily.
- Treat each machine and each application separately.
- If in doubt, seek advice from the independent OELCHECK experts.
- Check your machines with oil and grease analyses, especially during the changeover phase.
- Never place food contaminated with NSF-H-1 products on the market.